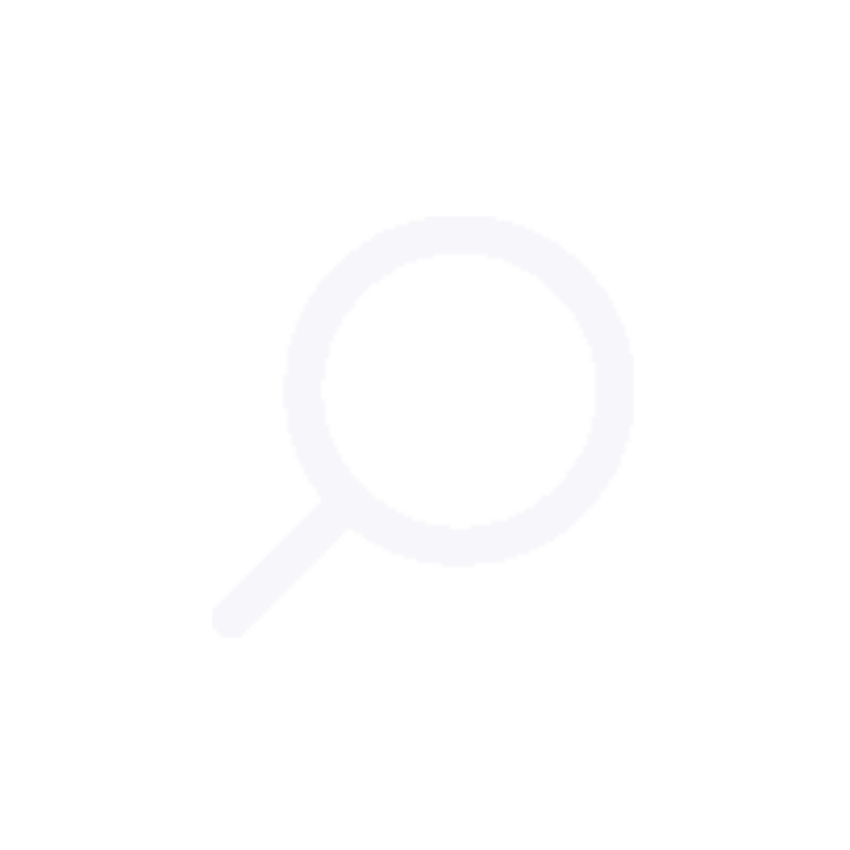
TEXO Engineering and Fabrication was awarded the project to construct the commercial O2 tidal turbine. Once operational, the O2 will be the most powerful turbine in the world. The O2 will is a 72m long floating superstructure, supporting two 1 MW turbines at either side for a nameplate power output of 2MW, at a tidal current speed of 2.5 m/s. With rotor diameters of 20m, it has a 600sq metre rotor area, the largest ever on a single tidal generating platform to date.
We fabricated the turbine at our Port of Dundee quayside facility, which was enlarged during the project. After initial fabrication indoors, the turbine was moved onto the quayside for the addition of legs, forward and aft hull sections and sails. The turbine will then be subject to land testing before being towed to its final position off the coast of the Orkney Islands.
One of the most complicated parts of the overall assembly phase was the complex operation of assembling each set of three large linkages, with connecting pins weighing up to 2 Te. Together with the main hydraulic rams, these complete assemblies weighed in at 18 Te each.
Once assembled, the linkages were lifted and manoeuvred so that they could be attached to the main hull structure and the leg tops. This involved horizontally jacking-in large machined pins to the line-bored clevises on the hull and leg sections.
The drawing of the operation and lift sequences was carefully prepared on CAD by TEXO Engineering and sequenced in a “story-board” to plan out the safe execution of this complex lifting operation. Both the port and starboard linkage and ram assemblies were successfully installed over two days, using twin 25T overhead cranes in the main fabrication shed.
“This enhanced tidal turbine design has been an outstanding renewables project for TEXO. Whilst there have been both technical and pandemic-related challenges, we have used our expertise and experience to keep the project moving, so that we can deliver the finished turbine early in 2021 when it will be moved by water to Orkney and installed in its operational location.”
Gary Mitchelson, Managing Director of TEXO Engineering and Fabrication