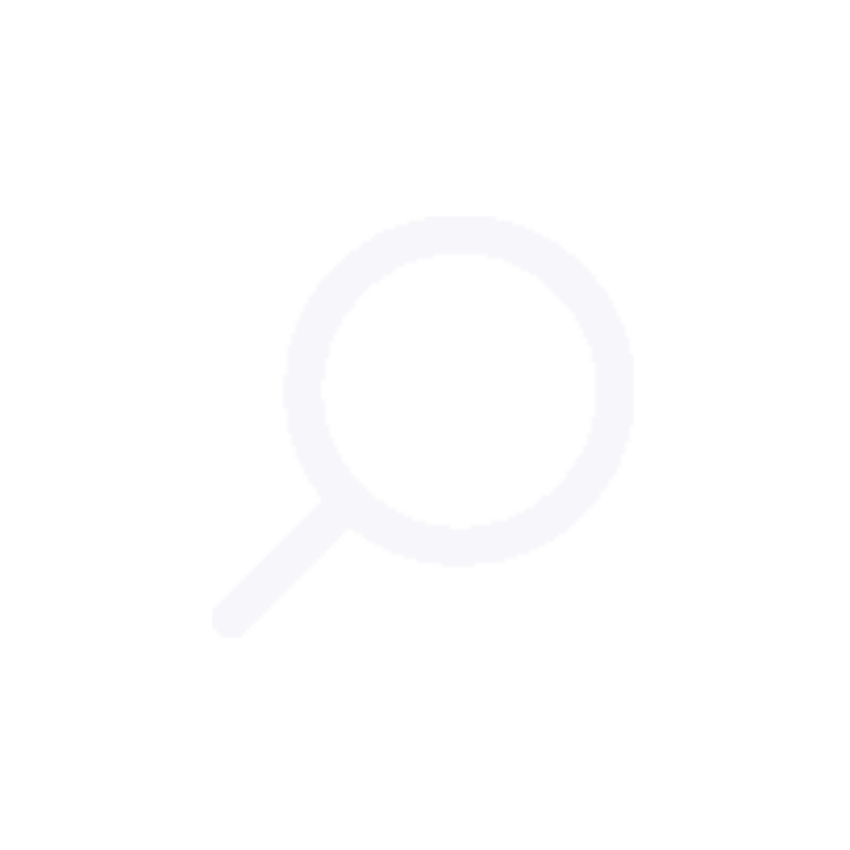
Our UAS Precision inspection service delivers minimal tolerance, repeatable and stable visual data sets, facilitating the detailed examination and thorough inspection of client assets.
Combined with our innovative, interactive and analytical software platforms for asset management, our inspections translate acquired visual data sets into actionable and quantifiable information, allowing structured O & M scheduling and planning.
Operating multiple RPAS, integrated with advanced and industry leading payload technologies, we are able to ensure our extensive, innovative and scope specific visual systems are correctly deployed, taking into consideration all factors, environmental, client deliverables and location.
We offer the most extensive range of precision inspection platforms in industry. Our precision inspection fleet consists of manifold 36, 42 and 50mp UAS integrated camera systems, through to industry leading and bespoke 100 megapixel(mp), camera technology.
Integrated into our own customised UAS platforms, via unique, tri-mounted gimbal configurations, our 100mp systems ensure unrivalled inspection camera orientation and image capture, providing an entirely new and unsurpassed level of high definition image acquisition and subsequent post inspection analysis.
The primary and standardised RPAS system utilised by our precision inspection teams however is the ASCTEC Falcon 8 and INTEL Falcon 8 +, light weight and with superb performance and visual orientation parameters, it allows our UAS teams to operate in some of the most challenging environments, across multiple sectors.
Inspection package
30x optical zoom camera and FLIR TAU 640 Thermographic dual payload.
12x optical zoom HD live visual recording payload.
Survey package
Alpha 7r / Alpha 7r2 36 – 42mp – camera payload.
The above payload configurations of the F8/8+ ensure the capture of high definition and accurate data. All of our Falcon 8 systems (8 & 8+) have been ‘in house’ optimised, with integrated tri-laser measurement systems, providing quantifiable scalability of acquired images to millimetre precision, for ongoing comparative asset analysis.
As a leading operator within the UAS industry, we deploy under one of the most expansive PfCO’s issued by the CAA, allowing us to operate in areas otherwise denied to other operators, such as major cities and congested and/or sensitive airspace.
We also deploy, a number of bespoke Tethered Systems, allowing operational deployment in areas previously requiring extensive permissions.
Offering a solid power line to the RPAS for power and an interference proof data link to the ground paired with shielded electronics, allows the RPAS to operate in areas of high frequency interference, completely immune to the effects.
Capable of 180x live magnification on a three-directional stabilised gimbal, this customised system offers extremely smooth data capture in both video and still formats. The tether systems allow for operational ceiling deployment to both 50m and 120m, enabling prolonged flight for maximised utilisation of flight windows.
All onshore precision inspections are fully supported by our fleet of aerial operations support command vehicles.
All aerial operation support vehicles are fully equipped and integrated with extensive charging facilities to ensure maximised flight duration for our UAS systems and comprehensive IT and visual infrastructure for pre mission planning, ‘in-flight’ and client led mission control and post inspection survey analysis and sign off.
ThermographicUtilising our extensive range of thermal imaging cameras, we undertake a wide range of detailed and quantifiable thermographic survey applications.
Our thermal survey and Inspection UAS teams are trained and certified to minimum ABBE Level 4 (efficiency surveys) and PCN Level 2/3 (BINDT) – ensuring acquired data can be quantified and interpreted.
Systems such as our dual view Falcon 8 equipped with FLIR TAU 640 & LUMIX 30 x optical zoom camera, ensure that both the visual and thermal aspect of the inspection/Survey can be carried out simultaneously and efficiently.
For more detailed thermographic applications, Texo DSI Ltd also have extensive integrated platforms, such as manifold M600, fully equipped with Micro Epsilon TIM 640 LW/Sony ALPHA 7R2 dual payloads with factory calibrated, interchangeable lenses tailored to suit varying inspection requirements and criteria.
We also deploy an extensive range of bespoke ICI integrated Radiometric thermal camera systems on both untethered and tethered UAS platforms, equipped with unique software applications allowing seamless ground to air integration for precise and specific client thermal work scopes.
Our Thermal systems have an extensive range of applications:
Our UV Corona System works by using UV spectrum data capture sensors to allow for visualisation of effects, invisible to the naked eye.
When an electrical component suffers a degradation in insulation and subsequent exposure, the air around the fault becomes ionized. UV Corona can detect these faults and allow operators to act before catastrophic failure becomes imminent.
Mounting this system to our UAS delivery platform allows us to reach inaccessible sites, thus limiting extensive risk to personnel and also ensuring inspection on a more regular basis. Our system can be deployed almost instantaneously to check for damage at key infrastructure and quickly help clients to best allocate resources.
Survey Grade LiDARTexo Drone Survey & Inspection Ltd are the ONLY operator globally, to facilitate UAS integrated SURVEY GRADE LiDAR (Light Detection and Ranging).
After extensive research and cross discipline skill accumulation, Texo DSI Ltd has managed to develop multiple, UAS integrated scanning systems, delivering consistent sub 3mm accuracies.
Integration into our custom-built UAS delivery platform incorporated with multiple redundancies, offers unrivalled safety and performance.
Using bespoke REIGL high accuracy (HA) scanning systems with optimised IMU, 1 million measured points per second (MPS) deliver consistent and high accuracies of sub 3mm at 30 – 80m from the target.
Flying at a higher altitude will result in a minimal decrease in accuracy but will facilitate increased area coverage.
In-house, post survey data optimisation is conducted where applicable and thus enhance precision and asset visualisation. Our Virtual Reality (VR) and asset integrity software platform, TEXZONE, provides our clients with a powerful post data acquisition, user interface for asset management and analysis.
Finally, our scanning technologies have also been designed to facilitate increased operational deployment via vehicle and man portable configurations at exacting accuracies, encompassing any area of operation and ensuring total asset and area coverage.
All onshore LiDAR surveys are fully supported by our fleet of aerial operations support command vehicles.
All aerial operation support vehicles are fully equipped and integrated with extensive charging facilities to ensure maximised flight duration for our UAS systems and comprehensive IT and visual infrastructure for pre mission planning, ‘in-flight’ and client led mission control and post inspection survey analysis and sign off.