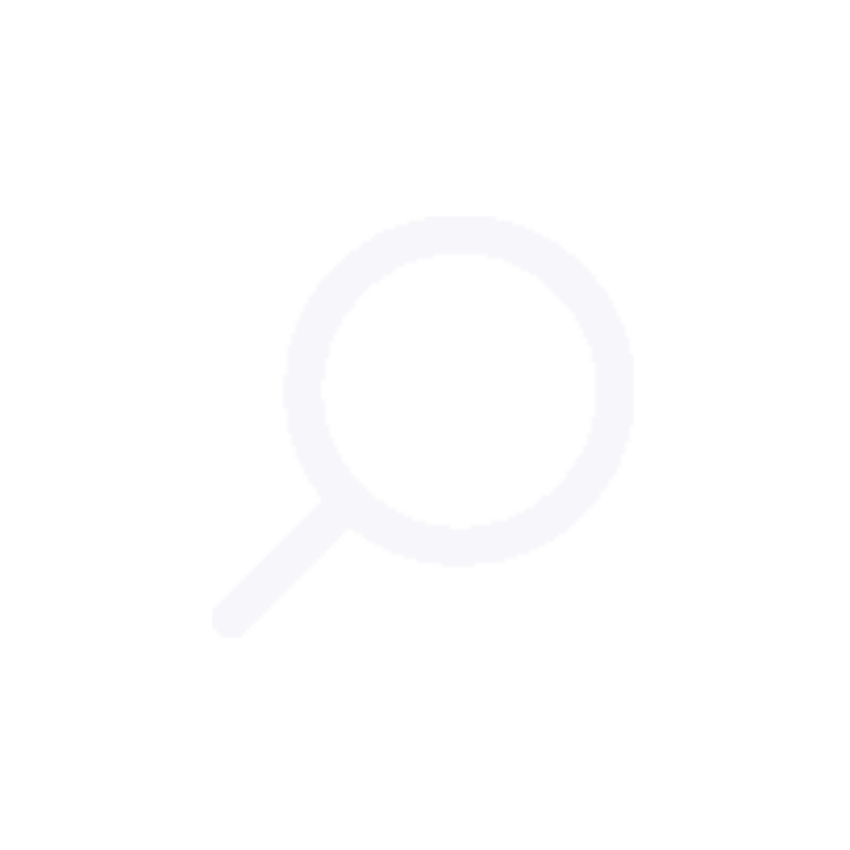
After extensive research and development by our in-house Innovation Hub, Texo Drone has successfully developed and deployed the Texo UAS Thickness Gauge; designed for thickness measurements to be performed at height without the need for traditional manual access solutions.
A first for the industry – the custom-built UAS is designed with state-of-the-art multiple propulsion and flight control system redundancies to ensure the safest operation even in the event of failure of a thrust component or flight controller.
The system has been designed to undertake a wide range of thickness measurement applications and is able to ascertain precise measurements on both flat and curved surfaces, including external and internal FPSO, fuel tank storage vessels etc.
This UAS integrated UT payload has been deployed across a wide range of sectors, including both offshore and onshore Oil & Gas, wind turbine structures, telecoms and maritime assets.
With the ability to indicate, via a unique spot identification system, all UT missions are precise in acquisition and instantaneous in capture and delivery. The measurements are transmitted wirelessly in real time to a PC or laptop up to 300 metres away.
All UT UAS operations are overseen by Texo’s accredited and certificated NDT payload technicians, ensuring accurate data set capture and validation of acquired measurements.
Inspection data is combined with a precise photogrammetric visual overlay of the completed survey, pinpointing exact measurement locations on the structure/surface to an accuracy of sub 10mm – therefore providing clients with verified inspection data.
The system benefits from a number of highly advanced features including: Multiple Echotechnology ensuring just the metal substrate is measured.
All probes have Intelligent Probe Recognition (IPR), which automatically adjusts settings in the gauge at the same time as transmitting recognition data – the result is a perfectly matched probe and gauge for enhanced performance.
Additionally, the Automatic Measurement Verification System (AMVS) ensures only true measurements are displayed, even on the most heavily corroded metals.
All of these enabled technical features ensure seamless transition between manual and UAS inspection methodology.
Bespoke dedicated software, acts as the interface between the UAS and the inspector’s PC allowing storage of measurements from the gauge in either a grid or string format, which can be used later in other proprietary programs.
In addition to our external UAS UT systems, we are currently in advanced field trials of our Internal UAS Integrated UT Gauge.
This UAS UT system has been specifically designed for internal measurement and inspection scopes, with bespoke illumination and flight control.
Field trials will be completed end Q2 18 and deployed and cleared for commercial mission scopes Q3 2018.
Heavy Lift UAVSky Crane WinchOur world and industry first, UAS integrated winch system for the supply and retrieval of loads up to 10kg is a game changer in terms of safety and efficiency.
With fully integrated and adjustable FPV (first person view) for the pilot operator, our pilot is able to deliver with great accuracy and safety, loads to personnel on high structures and difficult to reach locations.
With the ability to take off from multiple locations, both offshore and onshore, our system decreases the need and the associated risks of embarkation and disembarkation from offshore turbines to vessel and the necessity for personnel to climb tower structures for tool and small parts retrieval.
Our system is and has been utilised upon construction sites and for both offshore vessel to vessel and vessel to platform operations.
Designed with an electronic and pilot operated hook delivery system and tension maintained 5m line, to eliminate swing factors, our pilot is able to deliver loads to personnel safely, accurately and efficiently.
Our UAS winch supply drop system is proof yet again of our innovation and is yet another Texo Drone developed UAS system, designed for real world applications and the increased safety of personnel.
Tethered SystemsSpecific difficulties to be overcome by drone operators are current legislation and flight times.
Tethered systems offered by Texo DSI Ltd remove such difficulties. With the ability to remain airborne for several hours, even days, due to the constant supply of power via the tether and an uninterrupted data transfer facility to the ground, these systems offer the perfect solution when constant monitoring is required.
With our tethered platforms carrying dual payloads, a whole host of applications can be accommodated, such as security and surveillance, Sports coaching optimisation and even crisis management.
The reduction in legislation due to its tethered application, allows the system to operate in crowded environments, utilised as an elevated observation platform and other security/surveillance applications.
Our tethered systems have also been applied to emergency telecommunications support and are currently being optimised and developed in conjunction with our existing telecommunications partners, to provide a rapid deployment facility to ensure continued Network Uplink, post incident.
3D/GeospatialWith a diverse RPAS fleet, incorporating both fixed wing Q200 surveyor pro with fully integrated PPK and various Multi rotor platforms, Texo DSI Ltd are able to fulfill a wide range of photogrammetric applications.
Utilising multiple images of an area or object, our diverse and advanced software applications and trained technicians can generate accurate 3D models for a multitude of projects. Measurements are acquired via multiple data points of a specific area or object from different views and matching them up.
This technique is widely used by Texo DSI Ltd for volumetric analysis and certain site/structure data generation where accuracy is surpassed only by OUR survey grade LiDAR Platform.
Orthomosaics are the stitching of multiple aerial shots to produce a signal image for use in multiple sectors. Helpful in infrastructure planning and largescale site planning.
Internal UAV InspectionOperations in confined, unlit and hazardous spaces have long been a logistical headache for plant engineers, often requiring extensive planning to ensure requisite health and safety conformity, alongside the subsequent and associated cost implications for conventional human access.
Due to the necessary safety protocols and subsequent limited timescales of human entry, to inspect the confined space area, data capture prioritisation can lead to the potential overlooking of minor deficiencies, ultimately leading to failures in systems and the dreaded ‘fix on fail’.
Our UAS internal systems are integrated with dual visual and thermal sensor systems, paired with super bright LED lighting to allows for the safe operation in confined, unlit spaces.
High definition visual data at 0.2mm per pixel allows detailed examination of structural fabric and componentry, whilst rapid deployment and manoeuvrability for tanks and other vessel structures 6m x 25m in as little as 30 minutes.
To prevent damage to the RPAS, a carbon fibre anti-collision encapsulation system is utilised, allowing for the RPAS to come into direct contact with surfaces to maximise data quality whilst ensuring no damage is sustained to either the asset or the RPAS.
With the high manoeuvrability of RPAS systems, inspection & surveys can be rapidly altered if unexpected features arise during live inspections.
Without the need and time to be spent on the development and installation of other engineering access solutions, operational durations are maximised and disruptions decreased, all the while limiting the exposure of human resources in hostile environments.
To ensure maximised operational duration & deployment, our internal UAS solution utilises a unique and customised ground based mini all-terrain track vehicle in areas of signal interference.
This mobile antenna deployment vehicle makes it possible to carry an extended antenna relay system into the base of large tanks and other vessels. This allows for uninterrupted communication between the RPAS operator and the UAS system, providing increased visual facilitation in areas previously considered unreachable.
The mobile deployment system is combined with a visual, infrared and image intensifier camera (NVI) to allow monitoring of the UAS whilst deployed.
In summary, our internal inspection RPAS allows engineers to deliver asset inspection and subsequent structural report generation efficiently, accurately and more importantly with increased SAFETY.
Optical Gas Imaging (OGI)Texo DSI Ltd has acquired two G300a Optical Gas Imaging thermal systems. Integrated into our own custom-built, multi redundancy UAS platforms, the G300a can detect 20 confirmed types of gas leaks and allow for rapid gas leak identifications.
Texo DSI Ltd are currently utilising two OGI systems (TEXO G.O.L.D SP1 & TEXO G.O.L.D DP2), operating within the industrial and domestic environment. Using a maximised gain on the G300a, gas leakage can be detected within the lower pressurised Domestic gas system, ensuring swift identification of leaking infrastructure and the subsequent repairs to be implemented.
Some of the detectable gas types are extremely hazardous and using the UAS allows for the removal of human operators near to the source during primary investigation.
Our UAS delivery systems (TEXO G.O.L.D SP1 & TEXO G.O.L.D DP2) have been built to encompass a platform built to operate in some of the most safety conscious environments, with multiple redundancies beyond the basic accepted standards.
HyperspectralHumans see in three visible bands, red, green and blue. We use these to see our world in colour and distinguish between features, by the colours our eyes detect. Hyperspectral systems used at Texo DSI Ltd can detect a plethora of spectrums allowing for observation of up to 369 spectral bands.
This allows for bands to be configured together and compared to multiple spectral libraries, to identify the vast majority of substances unique spectral signatures. Many applications exist with key soil nutrient quantification, disease detection and chemical composition of plants in agriculture. Mineralogical identification in geological mapping and potential identification of areas of commercial mineral exploration has long been a large use of hyperspectral data.
Certain hazardous materials can even be detected. Libraries are currently being compiled to detect possible changes in vegetation, to indicate sub surface gas leak detection at hydrocarbon drill sites. An area of developing interest to Texo DSI Ltd, is the ability to detect asbestos bearing materials within the construction industry and public sector. We have specified a custom-built, industry leading Hyperspectral UAS delivery platform.
MultispectralMultispectral data has been long established as a useful tool. Conventionally satellite or plane/helicopter mounted, it has been long proven in a number of commercial and industrial applications.
With integration into advanced UAS platforms, such as our QUEST UAS PRO 200 Fixed Wing Systems, it can now be deployed quickly and at a fraction of the cost making it commercially viable across a range of sectors.
Using multiple bandwidths of light beyond the visible spectrum multispectral can detect and quantify a range of data across a wide range of applicable sectors.
Texo DSI Ltd primarily operates our multispectral systems within the agricultural sector, allowing for precision agriculture to identify areas of crop stress and poor health. This allows farmers to initiate changes to field maintenance plans.
Watering schedule and fertiliser application are often adapted, producing an increase in efficiency and production, whilst often seeing a substantial decrease in resources over allocation.