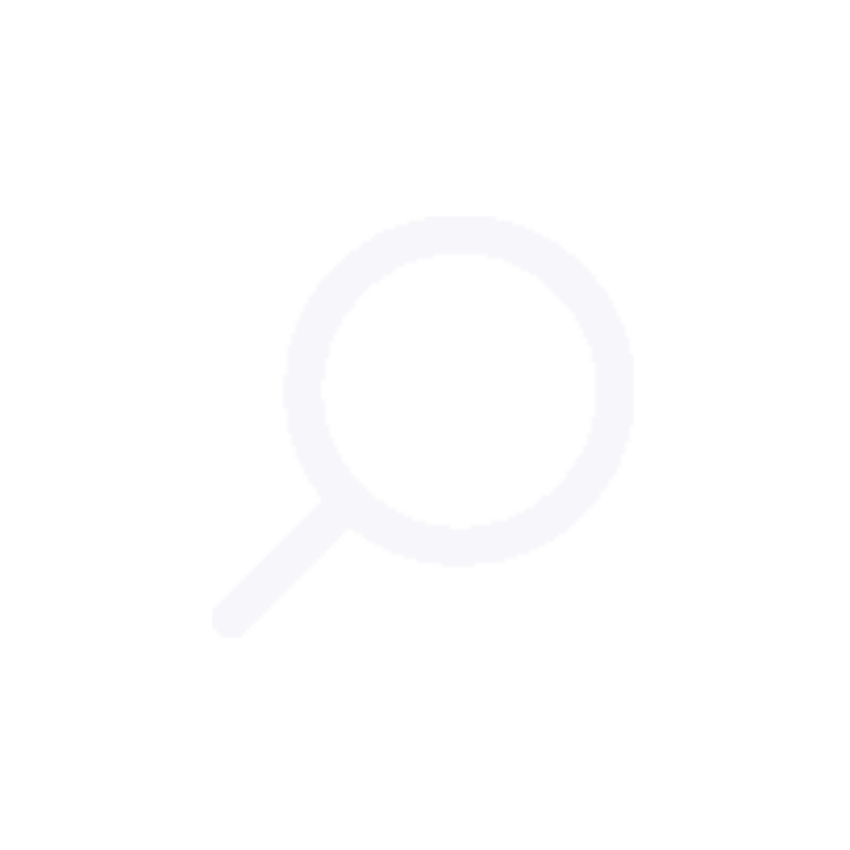
The client needed to carry out a confined space inspection of a ducting vent leading from a silicon mill. This inspection had to check for any damage to the lining which would affect the structural integrity and result in a possible “blow out” of the ducting, because of the highly abrasive silicone powder.
The report detailing the observed damages would be analysed by the client’s engineers to help them make a plan of action for the next stage in the project.
We used our class-leading internal confined space UAS system, which offers dual visual and thermal sensor payload paired with super bright LED lighting to allow for the safe operation in hazardous confined unlit spaces. This internal inspection system configuration allows for detail of 0.2mm per pixel.
Using this system, we carried out an internal visual inspection of an Outlet Ducting at the chemical processing plant. Five flights were flown gathering 26 minutes of video footage.
Due to the nature of the space and its contents a fire watch had to be established. The entrance way was also considered as a confined space, which meant that our system had to be initialised outside and flown into position for the survey. Utilising the boarded level below and the entry ducting as a take-off platform gave the base line for elevation data.
The orientation of the platform was designated with respect to the orientation from inside the ducting. This allowed for each fault detected to be located accurately within the duct and ensure that there was no clustering of minor faults which could contribute to a major fault.
The report, subsequent images and raw footage were all hosted on Texo’s custom built Texzone Client Portal which allowed for easy access to the data and its distribution to all levels of the organisation.
The project reporting feature allowed for efficient cross-department cooperation, with multiple engineers able to review the data and provide input.